Lograr 30 caballos de potencia más en un motor es posible gracias a la impresión aditiva o en 3D
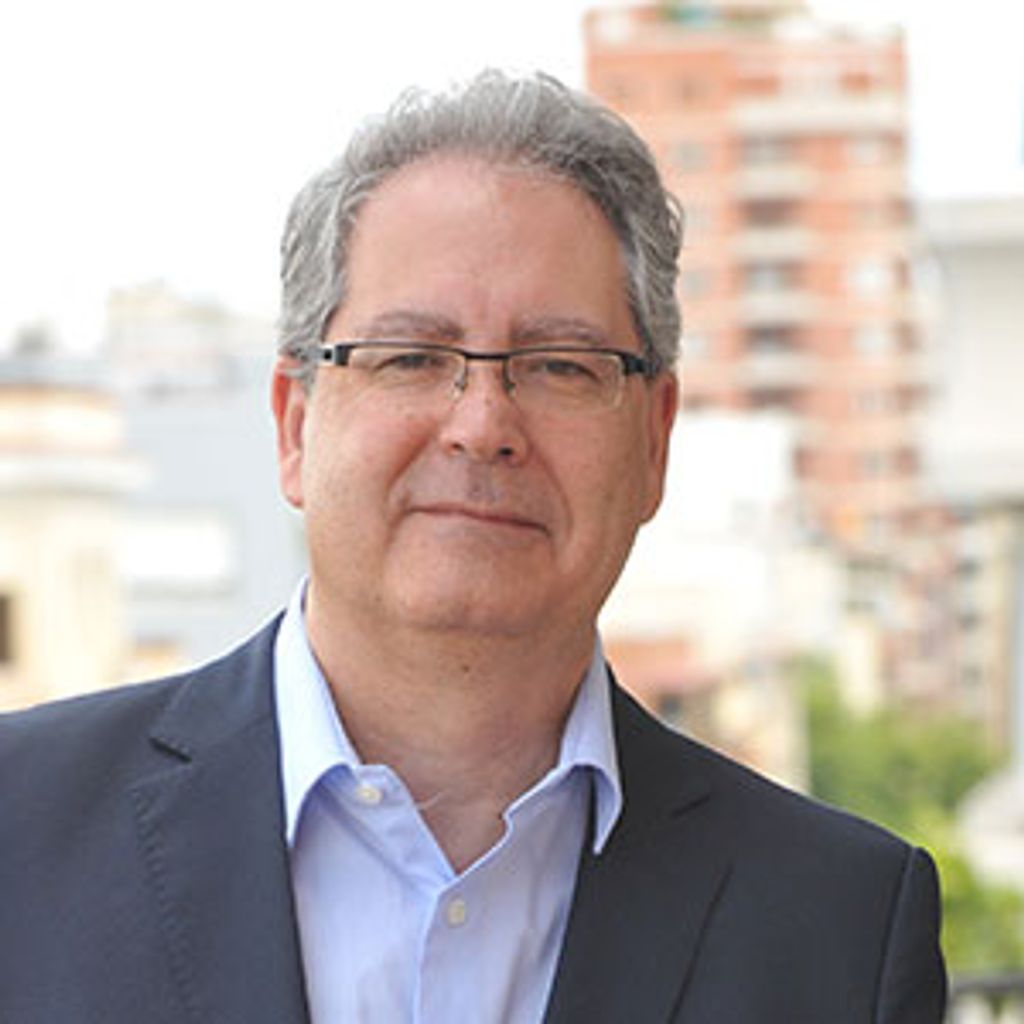
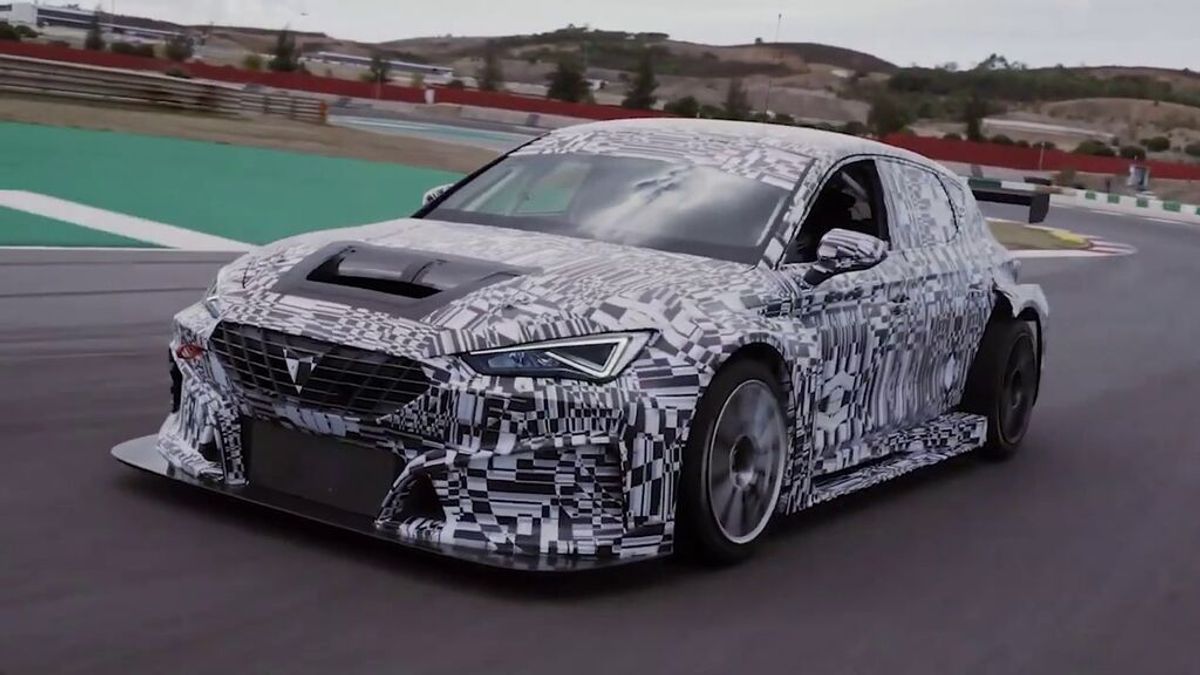
Muchas de las 7.000 piezas que de media monta un coche son susceptibles de ser hechas mediante impresora de adición de material
La reducción de costes y plazos puede llegar al 90% sobre todo en series pequeñas y muy especializadas
Su precisión puede llegar a las centenas de micras y las piezas tienen el grado industrial y pasan todas las homologaciones
Si les hablo de impresión aditiva es muy posible que ustedes no sepan a qué me estoy refiriendo. Sin embargo, si les hablo de la impresión 3D, ya es otra cosa. Por eso, tengo un amigo que dice que este es el término “marketiniano” más importante para la industria de los últimos tiempos. Y lo dice en el doble sentido, ya que es importante para la impresión 3D, pero va a ser también una de las disrupciones industriales que más van a cambiar la fabricación en los próximos años.
Consultoras como McKinsey esperan, por ejemplo, que su impacto económico ronde nada menos que los 250.000 millones de euros en 2025. Wohlers Associates dice que su crecimiento medio ha superado el 20% en los últimos cuatro años. Y uno de los sectores en los que su penetración está siendo mayor es precisamente la automoción, según esta misma consultora, pues en el podio de las industrias que más la utilizan se sitúa en segundo lugar, solo por detrás de la de la fabricación de maquinaria (19,8%) y por delante de la industria aeronáutica.
MÁS
Los fabricantes de coches no dejaron pasar la oportunidad de incorporar sus ventajas muy pronto. Este modo de procesamiento de piezas surgió hace algo menos de 30 años. Pero, por ejemplo, Seat lleva nada menos que quince años incorporándolo ya a sus procesos en España. Y como ella prácticamente todas las grandes marcas de coches y también de motos como BMW, Ford, Hyundai, Opel, Porsche, Renault, Volkswagen, Volvo, Honda, Polaris... o estudios de diseño como Italdesign.
Sumar y no restar sería el resumen de lo que marca la gran diferencia de este método de generación de piezas, ya que la fabricación tradicional es sustractiva. Es decir, el proceso comienza con más material del que finalmente va a ser necesario, para ir eliminando lo que no se quiere hasta llegar a la forma final. Pensemos por ejemplo en un palo al que vamos quitando madera con una navaja para sacarle punta. En la fabricación 3D este proceso es justo el contrario. El material se va añadiendo en una máquina impresora capa a capa, a medida y de forma selectiva. Y eso se hace partiendo de un modelo digital prediseñado con toda exactitud en tres dimensiones. Un ejemplo podría ser la construcción de una casa en la que se van levantando paredes con ladrillos desde la nada. Pero, además, hay toda una serie de ventajas diferenciadoras.
1 - Menos costes
La reducción de costes por pieza puede llegar a situarse entre el 40% y el 90%. ¿Los motivos? La no necesidad de moldes para generar las piezas reduciendo o eliminando la necesidad de utillajes y herramientas. La reducción de materiales, piezas y de métodos de ensamblaje (pegamentos, puntos láser...) pues la pieza se genera completa en formas que mecánicamente sería imposible, a veces ni siquiera con piezas unidas.
2 - Reducción de plazos
La producción de piezas se realiza mucho más rápido al saltar directamente del “plano” en 3D a la pieza fabricada. Puede suponer un 95% del plazo de producción, máxime cuando “bibliotecas virtuales” de piezas permiten basarse en diseños ya previamente iniciados o creados, ahorrando mucho tiempo. Los expertos hablan de pasar de semanas a días e incluso a horas.
3 - Mayor productividad
Es posible mantener una fabricación prácticamente desatendida “24x7” es decir, con mínimas interrupciones (para recarga de materia prima, por ejemplo).
4 - Ligereza
En la gran mayoría de las ocasiones las piezas se generan mediante material termoplástico de grado de ingeniería, igual de resistente que el metal, pero mucho menos pesado. Y es mucho más sencillo generar piezas con huecos para que pesen menos. Pero se usan también metales y materiales cerámicos.
5 - Seguridad y salud
Es obvio la menor generación de peligros para los operarios, que quedan aislados de chispas, elementos móviles o cortantes... Además, se reducen los problemas derivados de malas posturas de los empleados en los procesos, evitando otro de los grandes problemas de la fabricación industrial.
De clips a asientos
Pero, ¿cuáles son las principales aplicaciones que se están dando ahora mismo en automoción? Las dos más importantes son la generación de herramientas para realizar montajes en fábrica o talleres y, por supuesto, la de piezas ya completas para su instalación en vehículos. Pongamos algún ejemplo.
Porsche en colaboración con Mahle y Trumpf realizaron unos pistones para el 911 GT2 RS. En ellos pudieron generar unos conductos para su refrigeración que hubieran sido imposibles de fabricar de una forma mecánica debido a sus intrincadas formas interiores. Esto, junto a su menor peso y a la optimización de la estructura para las cargas soportadas, supuso un incremento de potencia en el motor de nada menos que 30 caballos de potencia, mejorando un 7,5% el rendimiento del vehículo. Son datos de Andrés Delgado, director de Soporte Técnico de la marca de Stuttgart. Otro ejemplo de Porsche son unas carcasas para motores eléctricos, con las que pudieron:
- Reducir el espesor de las paredes hasta 1,5 milímetros, doblando sin embargo la rigidez.
- Disminuir un 40% su peso, logrando que el peso total del conjunto del equipo descendiera un 10%.
- Eliminar 40 pasos del proceso de montaje, es decir, 20 minutos de tiempo.
- Una mejor integración con otros sistemas.
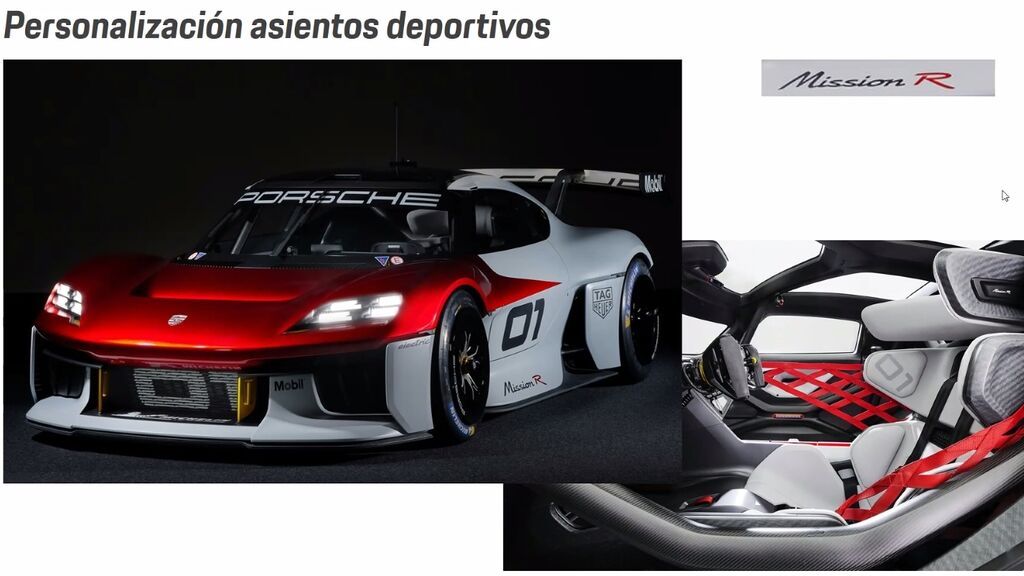
Más espectacular y comprensible sería la personalización para los asientos deportivos de su prototipo Mission R. Pero ya hay infinidad de pequeñas piezas y componentes que ya se realizan para diversos modelos y fabricantes. Desde posavasos o carcasas para espejos, hasta clips o tapones, un coche cuenta con entre 6.000 y 8.000 piezas y muchas de ellas se pueden fabricar mediante este proceso, según Víctor Barbero de Stratasys, quien también recuerda que el fabricante lleva varias temporadas colaborando con McLaren en sus monoplazas de Fórmula 1 para ofrecer ventajas competitivas en tiempo, peso y eficiencia.
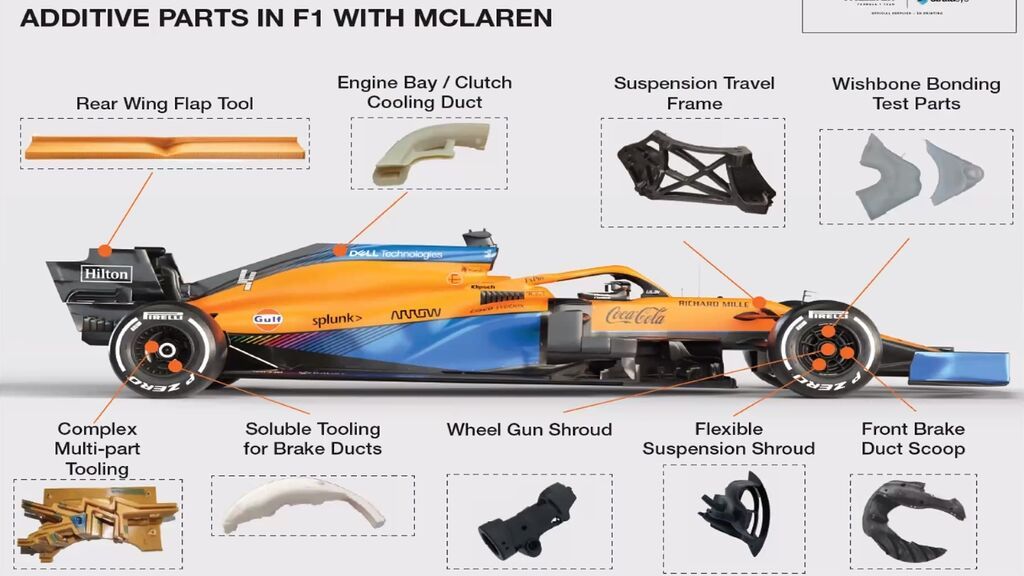
Otro ejemplo en la competición es el del Cupra León TCR sobre el que HP ha trabajado en conjunción con Cupra Racing. Pero quizá hablando de coches rápidos el ejemplo por excelencia sea el Chaos Ultracar del que ya hablamos hace unos días. En él las piezas fabricadas en 3D se multiplican, formando intrincadísimas piezas, de diseños casi de ensueño.
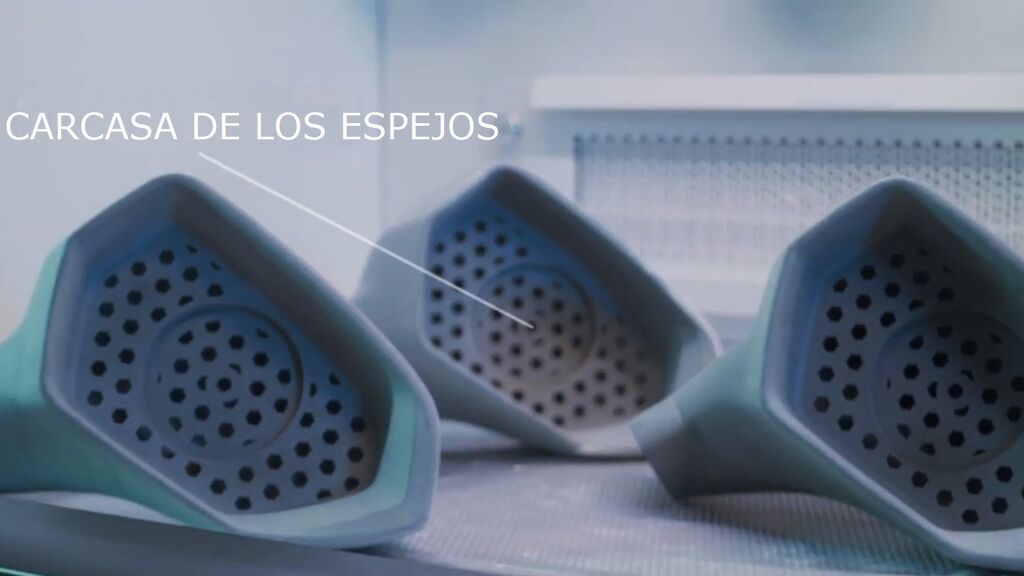
Piezas para clásicos
Pero las pequeñas series de piezas personalizadas son uno de los grandes terrenos de conquista de estos procesos, ya que supone abaratar sus costes de una manera drástica implicando un tanto por ciento mucho menor de mano de obra. Esta misma idea sirve para la restauración de piezas que ya no se fabrican, como por ejemplo piezas de coches clásicos.
Sus precios en la industria fluctúan desde los 15.000 € hasta los 300.000 € en el caso de las piezas más complejas. Estos dependen de la técnica a utilizar, la maquinaria de impresión necesaria, el diseño a realizar... También el material, pues cada día hay más posibilidades de impresión tanto en plásticos, como en metales e incluso en cerámicas. Y su calidad final es equivalente a las de las piezas producidas de otros modos, ya que tienen precisiones estimadas en centenas e incluso decenas de micras y pasan todas las homologaciones.
En cuanto a los procesos de impresión hay hasta 22 tipos diferentes, según Naiara Zubizarreta, de la Asociación Española de Tecnologías de Fabricación Aditiva y 3D (Addimat), que expuso en una presentación reciente de ASEPA. Algunos como la fusión con láser o arco eléctrico de material (metal, por ejemplo) mientras está siendo depositado (“Direct Energy Deposition”).
Otro aún más sofisticado se basa en soplar a través de una boquilla partículas a gran velocidad, lo que hace que vayan quedando pegadas unas a otras (“Cold Spray”). Aún más extravagante es la estereolitografía, que es un proceso químico que usa la luz y el oxígeno para la creación de piezas, haciendo que la luz vaya conformando el objeto mientras el cabezal va depositando el material (“Continous Liquid Interface Production”).
También es posible depositar unas nanopartículas de polvo cerámico o metálico disueltas en líquido que luego se va secando en las altas temperaturas de la cámara, haciendo que las partículas queden ligadas de forma absolutamente sólida (“Material Jetting”). La superposición de láminas o de hilo para formar volúmenes son ya más conocidas (“Sheet Lamination”).
Y Volkswagen va a aplicar otro tipo diferente que usa un adhesivo que se va aplicando a diferentes capas de polvo (“Binder Jetting”) para ciertas piezas de los pilares A (los que sujetan el parabrisas) en su todocamino compacto T-Roc. Lo van a hacer en colaboración con Siemens, porque según el miembro del consejo de administración de Volkswagen, Christian Vollmer “pretendemos hacer la impresión 3D aún más eficiente y más adaptada a su uso en las líneas de producción”.
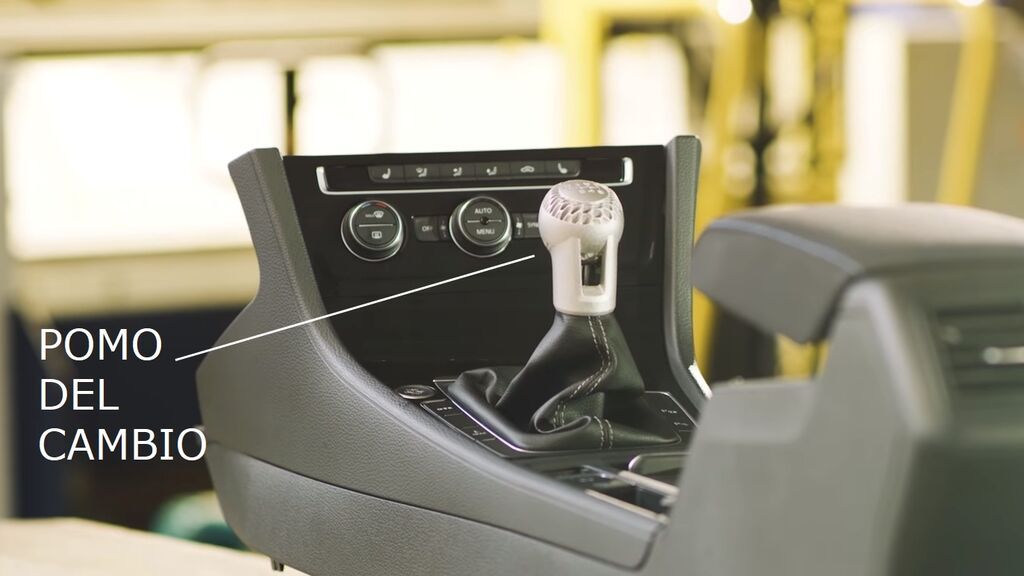
Y no será para menos, puesto que su intención es la de producir nada menos que 100.000 componentes al año en su fábrica central en Wolfsburg. Estos componentes para el T-Roc pesan la mitad que los fabricados de forma tradicional, según Volkswagen, una razón que ya les convierte en muy atractivos a ojos del fabricante alemán. Y eso que Volkswagen lleva 25 años estudiando y analizando este proceso y aplicándolo intensivamente sobre todo en la generación de prototipos de piezas, de los que la marca ya ha producido más de un millón de unidades. Volkswagen ya trabaja también con HP imprimiendo con metal y es uno de los fabricantes que más incide en esta nueva “herramienta” de producción.